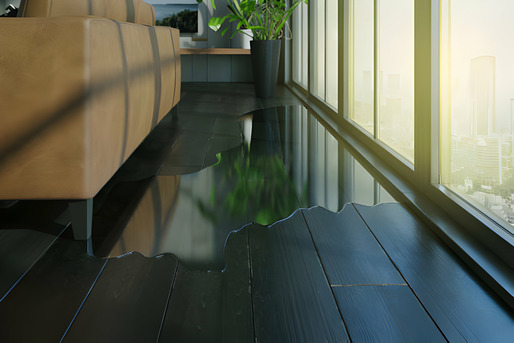
Water damage is a powerful enemy in the wide world of industrial facilities, especially when it comes to insulation. An industrial facility’s ability to withstand damage depends not only on the strength of its constructions but also on the quality of its insulation. If water seeps into this vital component, it can lead to problems with efficiency as well as possible threats to the facility’s overall safety.
In this extensive manual, we explore the tasks and skills involved in drying out water-damaged insulation in an industrial context. From comprehending the kinds of insulation that are frequently utilized in these establishments to putting specific drying methods into practice, our goal is to provide facility managers and maintenance teams with the knowledge required to restore insulation integrity and guarantee the industrial facility’s continuous operational excellence.
Water damage in an industrial plant is more than just a cosmetic issue; it eats away at productivity and efficiency. Insulation, which is critical to preserving energy efficiency and ideal temperatures, is compromised by water intrusion.
This guide serves as a road map for individuals attempting to traverse the difficulties presented by water-damaged insulation in industrial environments. It provides useful information on how to assess the degree of damage, select suitable drying techniques, and put preventative measures in place to strengthen insulation against potential threats. Join us as we explore the intricacies of industrial insulation drying and set out to protect the thermal stability and operational viability of industrial facilities.
Here is our related post on Practical Tips on How to Dry Out Water-Damaged Insulation in Commercial Properties
The Impact of Water Damage
1. Grasping the Severity
Acknowledge the severity of water damage. Water can compromise the integrity of insulation materials, diminishing their effectiveness and potentially leading to structural issues within the industrial facility.
2. Recognizing Potential Mold Growth
Recognize the risk of mold growth. Moisture-laden insulation creates an ideal environment for mold to thrive, posing not only health risks but also the potential for further damage.
3. Understanding Thermal Efficiency Loss
Understand the loss of thermal efficiency. Wet insulation loses its ability to provide effective thermal insulation, resulting in energy inefficiencies and increased operational costs for the industrial facility.
4. Evaluating Structural Risks
Evaluate potential structural risks. Prolonged water exposure can weaken building structures and compromise the safety and stability of the entire facility.
5. Identifying Material-Specific Challenges
Identify material-specific challenges. Different insulation materials react differently to water damage. Understanding these nuances is crucial for implementing appropriate drying methods.
Immediate Response Measures
Swift Identification of Water Source
Swiftly identify the water source. Locate and address the source of water intrusion to prevent further damage and ensure that the facility remains secure.
Implementing Emergency Water Extraction
Implement emergency water extraction. Utilize pumps and vacuums to remove standing water promptly, minimizing the duration of exposure and potential damage.
Isolating Affected Areas
Isolate affected areas. Prevent the spread of moisture by isolating damaged sections, containing the impact and enabling targeted drying efforts.
Promoting Ventilation
Promote ventilation within the facility. Increase airflow to expedite natural drying processes and reduce humidity levels, aiding in the preservation of insulation materials.
Conducting Initial Assessment
Conduct an initial assessment of the extent of damage. Thoroughly inspect insulation materials and the surrounding structure to determine the scale of the water damage.
See also our post on A Comprehensive Guide on Dealing with Water Damage in Historic Buildings which you will not want to miss.
Drying Techniques and Equipment
Utilizing Industrial Dehumidifiers
Employ industrial dehumidifiers. These powerful machines extract moisture from the air, expediting the drying process and reducing the risk of mold growth.
Implementing Air Movers
Implement air movers for enhanced ventilation. Strategically position air movers to improve air circulation and facilitate efficient drying, especially in confined or hard-to-reach areas.
Deploying Infrared Cameras
Deploy infrared cameras for moisture detection. Identify hidden pockets of moisture within insulation materials using infrared technology, ensuring a thorough drying process.
Leveraging Heat for Accelerated Drying
Leverage heat for accelerated drying. Introduce controlled heat to the affected areas, promoting evaporation and expediting the removal of moisture from insulation materials.
Employing Moisture Meters
Use moisture meters for precise measurements. Regularly assess moisture levels in insulation materials to track drying progress and identify any persistently damp areas.
Material-Specific Drying Strategies
Drying Fiberglass Insulation
For fiberglass insulation, prioritize thorough drying. Fiberglass may retain water, so ensure adequate airflow and ventilation to prevent lingering moisture.
Addressing Water-Logged Cellulose Insulation
For water-logged cellulose insulation, implement rapid extraction. Given cellulose’s propensity to absorb water, quick removal of excess moisture is crucial to prevent structural issues.
Ensuring Proper Drying for Foam Board Insulation
For foam board insulation, ensure proper drying without damage. Delicate foam materials may require specialized drying techniques to prevent distortion or compromise of thermal properties.
Monitoring Drying of Reflective Foil Insulation
Monitor the drying of reflective foil insulation. Regularly check for the removal of moisture between layers, ensuring the reflective properties are maintained for optimal performance.
Drying Out Mineral Wool Insulation
For mineral wool insulation, prioritize ventilation. As a denser material, mineral wool may require extended drying times, emphasizing the need for sustained airflow.
See also our post on How to Save Valuable Artwork from Water Damage
Post-Drying Inspection and Quality Assurance
Conducting Thorough Inspections
Conduct thorough inspections post-drying. Examine insulation materials, structural components, and surrounding areas to ensure that water damage has been effectively mitigated.
Assessing Structural Integrity
Assess structural integrity. Verify that the drying process has not compromised the stability of the industrial facility, addressing any structural concerns promptly.
Conducting Mold Risk Assessment
Conduct a mold risk assessment. Check for any signs of mold growth and implement remediation measures if necessary to maintain a healthy and safe environment.
Verifying Thermal Efficiency Restoration
Verify restoration of thermal efficiency. Ensure that insulation materials have regained their optimal thermal properties, contributing to energy efficiency within the facility.
Implementing Preventive Measures
Implement preventive measures. Identify and address potential vulnerabilities that led to water damage initially, preventing recurrence and fortifying the facility against future incidents.
Collaboration with Professionals
Consulting Industrial Hygienists
Consult industrial hygienists. Engage professionals to assess environmental conditions, ensuring that the facility meets safety and health standards post-water damage remediation.
Collaborating with Insulation Specialists
Collaborate with insulation specialists. Seek expertise to assess insulation materials and recommend any necessary replacements or enhancements for long-term performance.
Engaging Structural Engineers
Engage structural engineers. Have professionals evaluate the structural integrity of the facility, providing insights into any necessary repairs or reinforcements.
Coordinating with Water Damage Restoration Experts
Coordinate with water damage restoration experts. Leverage the specialized knowledge of professionals who can address both immediate and long-term water damage concerns.
Training Staff on Emergency Response
Train facility staff on emergency response. Equip personnel with the knowledge and skills to swiftly and effectively address water damage incidents in the future.
Developing Preventive Protocols
Instituting Regular Inspections
Institute regular inspections. Establish a routine inspection schedule to identify potential water intrusion points, enabling proactive measures to prevent water damage.
Implementing Water-Resistant Design Features
Implement water-resistant design features. Consider architectural modifications that enhance the facility’s ability to resist water damage, such as improved drainage systems and protective barriers.
Incorporating Waterproofing Measures
Incorporate waterproofing measures. Apply protective coatings or membranes to vulnerable areas, creating an additional layer of defense against water intrusion.
Educating Facility Personnel on Water Management
Educate facility personnel on water management. Foster a culture of awareness and responsibility, empowering staff to contribute to the facility’s overall resilience against water-related challenges.
Establishing Emergency Response Protocols
Establish emergency response protocols. Develop clear and actionable protocols for addressing water damage incidents, ensuring a swift and coordinated response.
Here is our post on Most Reliable Tips for Restoring Water-Damaged Roofing which you will not want to miss.
Conclusion
As we conclude this comprehensive guide on drying out water-damaged insulation in an industrial facility, envision a resilient and efficient industrial setting where water-related challenges are met with strategic solutions.
This guide aims to be your companion in navigating the complexities of restoring water-damaged insulation, safeguarding the structural integrity and thermal efficiency of your industrial facility. May these insights empower you to face water damage challenges head-on, ensuring that your industrial environment remains a bastion of productivity and safety.