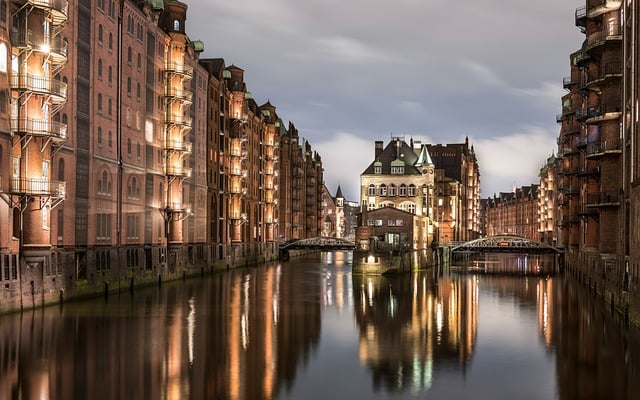
Commercial properties, bustling with activity, often face the challenge of water damage to insulation. Whether caused by leaks, flooding, or other unforeseen circumstances, addressing water-damaged insulation is crucial to maintaining a safe and efficient workspace.
In this comprehensive guide, we’ll delve into practical strategies and detailed steps on how to effectively dry out water-damaged insulation in a commercial property. From understanding the types of insulation to implementing drying techniques, this guide equips you with the knowledge needed to restore your commercial space to its optimal condition.
Water-damaged insulation not only compromises the structural integrity of a commercial property but can also lead to health hazards due to mold growth. Taking swift and decisive action is paramount to prevent further damage and ensure the well-being of occupants.
This guide aims to demystify the drying process, providing you with actionable insights to navigate the restoration of water-damaged insulation in your commercial establishment.
Here is our post on A Comprehensive Guide on Drying Out Water-Damaged Insulation in an Industrial Facility
Identifying Types of Insulation
Understanding the type of insulation used in your commercial property is the first step in devising an effective drying strategy.
Fiberglass Insulation
- Inspect for Saturation: Fiberglass insulation may not retain water as much as other materials, but it can still become saturated. Check for discoloration, sagging, or a musty odor, indicating water damage.
- Assess Mold Growth: Fiberglass can be prone to mold growth in damp conditions. Inspect for any visible signs of mold and be aware of the potential health risks associated with it.
- Remove Damaged Sections: If water damage is extensive, consider removing and replacing the affected fiberglass insulation to ensure thorough drying and prevent the spread of mold.
- Promote Air Circulation: Fiberglass insulation responds well to increased air circulation. Use fans and dehumidifiers to facilitate the drying process, ensuring a dry and mold-free environment.
- Monitor Over Time: Even after initial drying efforts, continue monitoring fiberglass insulation for signs of lingering moisture or mold. Address any issues promptly to prevent further damage.
Dealing with Cellulose Insulation
Identifying Water Absorption:
- Recognize Potential Saturation: Cellulose insulation, made from recycled paper, can absorb water and lose its effectiveness. Look for signs of dampness, clumping, or a distinct change in texture.
- Address Immediate Leaks: If water damage is localized, address the source of the leak immediately to prevent further saturation of cellulose insulation.
- Use Absorbent Materials: Place absorbent materials like towels or rags around affected areas to soak up excess moisture. This aids in preventing further spread of water within the insulation.
- Install Dehumidifiers: Cellulose insulation responds well to dehumidifiers. Introduce these appliances to the affected area to extract moisture from the insulation, promoting a faster drying process.
- Consult Professionals for Large Areas: In the case of extensive water damage to cellulose insulation, seek professional assistance. Commercial restoration experts can employ specialized techniques and equipment for thorough drying.
Addressing Water Damage in Foam Board Insulation
Assessing Water Resistance:
- Inspect for Water Infiltration: Foam board insulation is generally resistant to water, but external factors like leaks or flooding can still lead to damage. Inspect for any signs of water infiltration.
- Focus on Airflow: Due to its dense structure, foam board insulation benefits from increased airflow. Position fans strategically to enhance ventilation and expedite the drying process.
- Check for Delamination: Delamination, the separation of layers, can occur in foam board insulation after water exposure. If identified, consider replacing the affected sections to maintain insulation effectiveness.
- Utilize Perimeter Sealants: Ensure that the edges and joints of foam board insulation are properly sealed. This minimizes the risk of water seeping into vulnerable areas, preventing potential damage.
- Implement Gradual Drying: Gradual drying is crucial to prevent thermal shock in foam board insulation. Avoid applying excessive heat, allowing the material to dry at a controlled pace.
See also our post on A Comprehensive Guide on Dealing with Water Damage in Historic Buildings
Restoring Mineral Wool Insulation
Recognizing Water Absorption:
- Inspect for Water Retention: Mineral wool insulation can retain water if exposed to prolonged moisture. Check for changes in color, weight, or texture as indicators of water absorption.
- Replace Saturated Sections: If sections of mineral wool insulation are saturated, consider replacing them to ensure the overall integrity of the insulation system.
- Prioritize Ventilation: Adequate ventilation is key for drying mineral wool insulation. Use fans, open windows, and introduce dehumidifiers to promote efficient drying in affected areas.
- Address Mold Growth: Mineral wool, when wet, can become a breeding ground for mold. Act promptly to address any mold growth, ensuring the safety and health of occupants.
- Regular Monitoring: Even after initial drying efforts, monitor mineral wool insulation for lingering moisture. Regular checks and preventive measures can safeguard against future water damage.
Implementing Drying Techniques
Once you’ve identified the type of insulation and assessed the extent of water damage, employing effective drying techniques is essential.
Use of Dehumidifiers:
- Select Appropriate Size: Choose dehumidifiers based on the size of the affected area. Proper sizing ensures optimal moisture removal and facilitates a faster drying process.
- Position Strategically: Place dehumidifiers strategically to cover the entire affected space. Ensure good airflow around the devices for maximum efficiency.
- Monitor Humidity Levels: Regularly monitor humidity levels in the drying area. Adjust the settings on dehumidifiers to maintain optimal conditions for drying out insulation.
- Empty Water Reservoirs: Dehumidifiers collect water in reservoirs that need regular emptying. Stay vigilant in emptying these reservoirs to prevent overflow and maintain continuous operation.
- Use in Conjunction with Fans: Pairing dehumidifiers with fans enhances the drying process. Fans promote air circulation, helping dehumidifiers extract moisture more effectively.
Conducting Repairs and Replacements
Addressing water-damaged insulation often involves repairs or replacements to ensure the overall effectiveness of the insulation system.
Repairing Insulation:
- Patch Small Holes or Tears: For minor damages, use appropriate materials to patch small holes or tears in the insulation. This prevents further water infiltration and maintains insulation efficiency.
- Apply Sealants: Sealants can be effective in closing gaps or joints in insulation. Choose sealants suitable for the specific type of insulation to ensure a secure and water-resistant seal.
- Reattach Loose Insulation: If insulation has become detached due to water damage, reattach it using adhesive or fasteners. This restores the insulation’s integrity and effectiveness.
- Consider Professional Repairs: For extensive damage, consult with insulation professionals. They can provide tailored solutions, ensuring the thorough restoration of the insulation system.
- Replace Beyond Repair: In cases where water damage is severe and insulation is beyond repair, opt for replacement. This guarantees the installation of a fully functional and water-resistant insulation system.
See also our post on How to Prevent Water Damage to Furniture: A Comprehensive Guide
Preventive Measures for Future Protection
After successfully drying out water-damaged insulation, implementing preventive measures is crucial to avoid recurrence.
Address Underlying Issues:
- Identify and Fix Leaks: Regularly inspect the property for leaks and address them promptly. Fixing underlying issues prevents future water damage to insulation.
- Improve Drainage Systems: Ensure efficient drainage systems around the commercial property. Proper drainage minimizes the risk of water accumulation and subsequent damage to insulation.
- Implement Routine Inspections: Conduct routine inspections of insulation and the overall building structure. Identifying potential issues early allows for timely intervention and prevents extensive water damage.
- Educate Staff and Occupants: Raise awareness among staff and occupants about the importance of reporting leaks or water damage promptly. Swift reporting enables timely action and minimizes potential risks.
- Invest in Quality Insulation: Choose high-quality insulation materials and ensure proper installation. Quality insulation is more resistant to water damage and contributes to the longevity of the commercial property.
Conclusion
A methodical approach specific to the type of insulation being used is necessary to effectively dry out water-damaged insulation in commercial properties. This guide will provide you with the knowledge you need to navigate the restoration process, from identifying water damage to putting drying techniques into practice and carrying out repairs.
You may protect your business property from the damaging effects of water damage by being aware of the special qualities of various insulation materials and taking preventive action. When you set out to restore the insulation that has been harmed by water, keep in mind that promptness and diligence are your friends in maintaining the integrity of your business space.