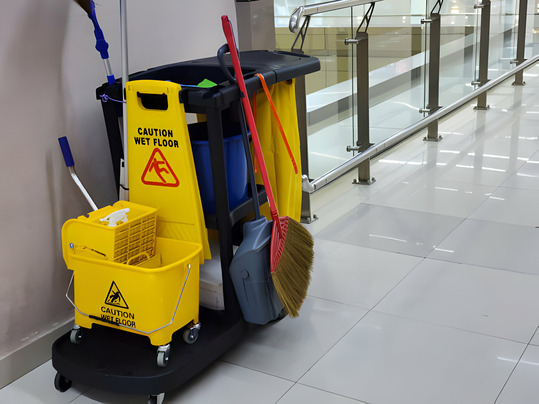
In the busy world of commercial spaces, cleanliness is essential, and the variety of cleaning tools utilized to keep spaces spotless and inviting is the foundation of this endeavor. Like any machinery, commercial cleaning tools need to be maintained to function at their peak, and this comprehensive guide explores the significance of preventive maintenance for commercial cleaning equipment, providing insights into how businesses can maximize the lifespan and efficiency of their cleaning arsenal.
Commercial cleaning equipment, ranging from carpet cleaners to pressure washers, plays a vital role in maintaining hygiene and appearance. Yet, neglecting their maintenance can lead to breakdowns, increased costs, and decreased productivity. In this article, we explore the key aspects of preventive maintenance for commercial cleaning equipment, providing practical advice to ensure these tools remain reliable workhorses in the pursuit of cleanliness.
See also our post on Professional Cleaning for Data Centers: Protecting Critical Infrastructure
Understanding Your Cleaning Equipment
Equipment Types and Variations
Commercial cleaning equipment comes in various types, each designed for specific tasks. Understanding the differences between vacuum cleaners, floor buffers, and carpet extractors is crucial for tailoring preventive maintenance to each piece of equipment.
Manufacturer Guidelines
Every piece of cleaning equipment comes with manufacturer guidelines. These guidelines provide valuable information on maintenance schedules, recommended procedures, and specific dos and don’ts. Adhering to these guidelines is fundamental for preserving warranty coverage and ensuring optimal performance.
Identifying Wear and Tear
Regularly inspecting cleaning equipment helps identify signs of wear and tear. Frayed cords, loose parts, or unusual noises during operation are indicators that preventive maintenance is needed. Early identification allows for timely intervention to prevent major breakdowns.
Usage Patterns
Understanding the usage patterns of cleaning equipment is essential. High-traffic areas may require more frequent maintenance, while sporadically used tools still benefit from periodic checks. Tailoring preventive maintenance to usage patterns ensures efficiency and cost-effectiveness.
Training Staff on Equipment
Well-trained staff contribute significantly to preventive maintenance. Educate cleaning personnel on the proper use, care, and minor troubleshooting of equipment. This knowledge empowers them to identify issues early on and report them for timely attention.
See also our post on The Role of Technology in Modern Commercial Cleaning
Regular Cleaning and Inspection
Daily Cleaning Routines
Incorporate daily cleaning routines into the schedule. Wipe down equipment surfaces, remove debris from filters, and empty collection bins. These simple tasks prevent the buildup of dirt and extend the life of cleaning equipment.
Filter Maintenance
Filters play a crucial role in many cleaning tools, from vacuum cleaners to air purifiers. Regularly clean or replace filters as per manufacturer recommendations. Clogged filters not only reduce efficiency but also strain the equipment’s motor, potentially leading to costly repairs.
Cord and Plug Inspection
Inspect power cords and plugs for any damage. Frayed or exposed wires pose a safety risk and can lead to electrical issues. Replace damaged cords promptly to ensure the safe operation of cleaning equipment.
Lubrication of Moving Parts
Moving parts, such as brushes and rollers, benefit from periodic lubrication. Applying manufacturer-approved lubricants reduces friction, minimizes wear, and contributes to smoother operation. Lubrication should be part of routine preventive maintenance.
Calibration Checks
Certain cleaning equipment, such as floor scrubbers, may have adjustable settings. Regularly calibrate these settings to ensure optimal performance. Misaligned or improperly calibrated equipment can lead to uneven cleaning and increased wear on components.
Scheduled Preventive Maintenance
Manufacturer-Recommended Schedules
Follow manufacturer-recommended preventive maintenance schedules diligently. These schedules often outline tasks such as belt replacements, motor inspections, and more. Adhering to these schedules minimizes the risk of unexpected breakdowns.
Inspection of Motors and Belts
Motors and belts are critical components in many cleaning machines. Regularly inspect these components for signs of wear, misalignment, or unusual noises. Timely identification of issues prevents major malfunctions and extends the lifespan of the equipment.
Battery Maintenance for Cordless Equipment
For cordless cleaning equipment, proper battery maintenance is essential. Follow guidelines for charging cycles, avoid overcharging, and replace batteries when needed. Well-maintained batteries contribute to consistent performance and avoid sudden shutdowns.
Calibration of Sensors and Controls
If cleaning equipment incorporates sensors or electronic controls, ensure regular calibration. Misaligned or malfunctioning sensors can lead to inefficiencies and erratic behavior. Calibration checks maintain precision in the equipment’s functionality.
Belt Tension Adjustment
Adjusting belt tension is crucial for equipment with belts, such as vacuum cleaners and floor buffers. Loose belts can slip or wear quickly, impacting performance. Regular tension adjustments, following manufacturer guidelines, prevent issues related to belt wear.
Addressing Common Issues
Vacuum Cleaner Blockages
Vacuum cleaners commonly face blockages in hoses, filters, or brush rolls. Regularly check for and address blockages to maintain optimal suction power. Prompt removal of blockages prevents strain on the motor and ensures efficient cleaning.
Floor Scrubber Squeegee Maintenance
Floor scrubbers rely on effective squeegees for proper water and solution recovery. Check and clean squeegees regularly, removing any debris or buildup. Well-maintained squeegees contribute to streak-free and efficient floor cleaning.
Pressure Washer Nozzle Inspection
For pressure washers, inspecting and cleaning nozzles is essential. Nozzle clogs or damage can affect water flow and pressure. Regular checks prevent uneven cleaning and potential damage to surfaces.
Carpet Cleaner Pump Checks
Carpet cleaners with pumps require regular checks. Inspect pump components for leaks, unusual noises, or reduced performance. Addressing pump issues promptly prevents damage to both the pump and the carpet cleaner.
Steam Cleaner Boiler Maintenance
Steam cleaners often feature boilers for heating water. Perform regular maintenance on the boiler, including descaling and cleaning. A well-maintained boiler ensures consistent steam production and extends the life of the steam cleaner.
Safety Practices
Power Disconnect during Maintenance
Always disconnect cleaning equipment from power sources before performing maintenance. This practice prevents accidental starts and ensures the safety of maintenance personnel.
Proper Storage Practices
When not in use, store cleaning equipment in designated areas. Avoid leaving equipment exposed to harsh weather conditions or high-traffic areas. Proper storage prevents damage and ensures equipment is ready for use when needed.
Personal Protective Equipment (PPE)
Provide and encourage the use of appropriate Personal Protective Equipment (PPE) during maintenance. Gloves, safety glasses, and other protective gear prevent injuries and promote safe handling of cleaning equipment.
Emergency Shutdown Procedures
Ensure staff is familiar with emergency shutdown procedures for cleaning equipment. In case of malfunctions or safety concerns, the ability to quickly shut down equipment minimizes risks and prevents further damage.
Staff Training on Safety Protocols
Train cleaning staff on safety protocols related to equipment use and maintenance. Educate them on the importance of reporting any issues promptly, fostering a culture of safety within the cleaning team.
See also our post on Sustainable Office Cleaning: Green Practices for a Productive Workspace
Equipment Upgrades and Replacements
Evaluating Equipment Lifespan
Regularly evaluate the lifespan of cleaning equipment. Understand when equipment is reaching the end of its operational life. Planning for replacements in advance prevents unexpected downtime and ensures continued efficiency.
Technological Advancements
Stay informed about technological advancements in cleaning equipment. Newer models may offer improved efficiency, eco-friendly features, and enhanced durability. Upgrading to newer technology can contribute to more effective cleaning practices.
Budgeting for Replacements
Incorporate equipment replacement budgets into long-term financial planning. Setting aside funds for replacements ensures that businesses can invest in the latest cleaning technology without compromising financial stability.
Trade-In Programs
Explore trade-in programs offered by equipment manufacturers or suppliers. These programs may provide incentives for trading in old equipment when purchasing new models, easing the financial burden of upgrades.
Environmental Considerations for Disposal
Follow proper environmental considerations when disposing of old equipment. Recycle or dispose of equipment in accordance with local regulations to minimize the environmental impact of electronic waste.
Documentation and Record-Keeping
Maintenance Logs
Maintain detailed maintenance logs for each piece of cleaning equipment. These logs should include dates of maintenance, tasks performed, and any issues identified. Proper documentation aids in tracking equipment history and planning future maintenance.
Equipment Manuals and Documentation
Keep equipment manuals and documentation in an accessible location. These materials provide valuable information on troubleshooting, parts replacement, and manufacturer recommendations. Referencing manuals aids in accurate maintenance practices.
Staff Training Records
Document staff training records related to equipment maintenance. Keep records of training sessions attended, skills acquired, and certifications obtained. Well-documented training ensures that all staff members are equipped to perform preventive maintenance effectively.
Replacement Schedules
Maintain clear replacement schedules for each piece of cleaning equipment. Document the expected lifespan, past maintenance history, and any signs of deterioration. Replacement schedules guide financial planning and prevent unexpected equipment failures.
Warranty Information
Keep track of warranty information for each piece of equipment. Understanding warranty coverage ensures that preventive maintenance practices align with manufacturer guidelines, preserving warranty benefits and reducing repair costs.
See also our post on Restaurant Kitchen Cleaning: Maintaining Hygiene Standards
Conclusion
In the busy world of commercial spaces, cleanliness is essential, and the variety of cleaning tools utilized to keep spaces spotless and inviting is the foundation of this endeavor. Like any machinery, commercial cleaning tools need to be maintained to function at their peak, and this comprehensive guide explores the significance of preventive maintenance for commercial cleaning equipment, providing insights into how businesses can maximize the lifespan and efficiency of their cleaning arsenal.