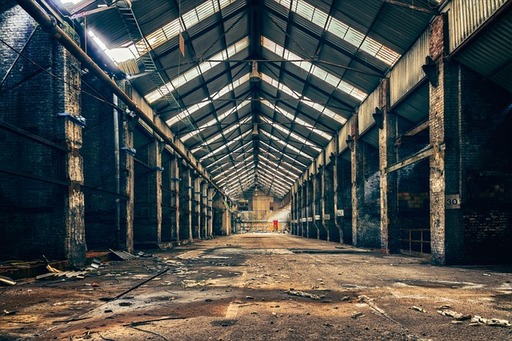
Warehouse organization and cleaning are not just routine tasks; they are the foundation of a well-functioning facility. In the fast-paced world of logistics and supply chain management, a warehouse’s efficiency is crucial to ensuring smooth operations. This comprehensive guide aims to delve into the nuances of optimizing efficiency through meticulous organization and cleanliness in warehouses.
A disorganized warehouse can cause chaos, delays, and higher operating costs; on the other hand, a well-organized and clean warehouse can increase productivity, decrease errors, and create a safer working environment. Let us explore the essential elements of warehouse organization and cleaning to maximize the potential of your facility. Warehouses are dynamic ecosystems where products come in and go out quickly.
Here is our post on Zero-Waste Bathroom Cleaning: Sustainable Scrubs and Sprays
Layout Optimization
Zoning for Functionality
Organize your warehouse into zones based on the type of products and their movement frequency. This zoning strategy ensures that high-demand items are easily accessible, reducing retrieval times and enhancing overall efficiency.
Logical Product Placement
Place products logically within each zone by considering factors like size, weight, and expiration dates. This logical arrangement minimizes the time spent searching for items, contributing to a more streamlined workflow.
Efficient Traffic Flow
Design the layout to facilitate smooth traffic flow. Avoid bottlenecks and ensure that pathways are wide enough for forklifts and other equipment to navigate without hindrance. A well-thought-out traffic flow plan prevents congestion and accelerates operations.
Utilization of Vertical Space
Maximize storage capacity by utilizing vertical space. Implement shelving and racking systems that allow for efficient stacking of goods, optimizing the available cubic footage in the warehouse.
Flexibility for Growth
Design the layout with scalability in mind. As your business expands, the warehouse should be adaptable to accommodate increased inventory without compromising efficiency. Plan for future growth to avoid major overhauls in the long run.
Inventory Management
Regular Audits
Conduct regular inventory audits to maintain accuracy. Identify discrepancies promptly, rectify errors, and update records to prevent fulfillment issues and enhance order accuracy.
ABC Analysis
Apply ABC analysis to categorize products based on their importance. Classify items into A, B, and C categories, focusing on high-value products to optimize their storage and retrieval processes.
Real-time Tracking Systems
Implement real-time tracking systems, such as RFID or barcoding, to monitor inventory movements. These systems enhance visibility, reduce the chances of errors, and enable quick responses to fluctuations in demand.
Forecasting Tools
Utilize forecasting tools to predict demand trends. By understanding future requirements, you can optimize inventory levels, preventing both overstock and stockouts.
Vendor Collaboration
Establish strong relationships with suppliers to ensure timely deliveries and reliable inventory replenishment. Collaborative planning with vendors fosters a smoother supply chain, minimizing disruptions.
See also our post on The Ultimate Guide to Cleaning and Caring for Your Outdoor Umbrellas and Canopies
Cleaning Protocols
Regular Maintenance Schedule
Implement a regular cleaning schedule to maintain a hygienic environment. Schedule routine inspections and cleaning sessions to prevent dust accumulation and potential safety hazards.
Clear Walkways and Emergency Exits
Keep walkways and emergency exits clear of obstructions. This ensures the safety of warehouse personnel and facilitates swift evacuation in case of emergencies.
Pest Control Measures
Implement stringent pest control measures to safeguard inventory and maintain a clean environment. Regular inspections and proactive pest management strategies are crucial for preventing infestations.
Equipment Cleaning Procedures
Regularly clean and maintain warehouse equipment to prolong their lifespan and prevent malfunctions. Dirty or malfunctioning equipment can significantly impede operational efficiency.
Waste Management
Establish an effective waste management system. Proper disposal of packaging materials, obsolete inventory, and other waste products contributes to a clutter-free environment and ensures a more organized workspace.
Employee Training
Safety Training
Prioritize safety training for warehouse staff. Ensure that employees are well-versed in safety protocols, handling equipment, and emergency procedures, minimizing the risk of accidents.
Cross-Training
Implement cross-training programs to enhance versatility among employees. Cross-trained personnel can fill in for absent colleagues, preventing workflow disruptions during peak periods.
Product Knowledge
Provide comprehensive product knowledge training to warehouse staff. This knowledge equips employees to handle items with care, reducing the likelihood of damaged goods and improving overall efficiency.
Communication Skills
Foster effective communication skills among team members. Clear communication minimizes errors, enhances collaboration, and ensures that tasks are completed accurately and promptly.
Continuous Improvement Training
Encourage a culture of continuous improvement by providing ongoing training opportunities. Equip employees with the skills and knowledge needed to adapt to evolving warehouse processes and technologies.
Technology Integration
Warehouse Management Systems (WMS)
Implement a robust Warehouse Management System to automate and optimize various warehouse functions. A WMS enhances accuracy, reduces manual errors, and provides real-time insights into inventory status.
Automation for Repetitive Tasks
Integrate automation for repetitive tasks, such as order picking and packing. Automated systems increase efficiency, reduce labor costs, and minimize errors associated with manual processes.
RFID Technology
Utilize RFID technology for tracking and managing inventory. RFID tags enable quick and accurate identification of products, enhancing inventory visibility and reducing the likelihood of errors.
Data Analytics for Decision-Making
Harness the power of data analytics to make informed decisions. Analyzing warehouse data can reveal trends, optimize inventory levels, and identify areas for improvement in overall efficiency.
Mobile Devices for Real-time Updates
Equip warehouse staff with mobile devices for real-time updates on inventory movements and order statuses. Mobile technology enhances communication and ensures that employees have access to critical information on the go.
Sustainability Practices
Eco-friendly Packaging
Opt for eco-friendly packaging materials to minimize environmental impact. Sustainable packaging not only benefits the planet but also contributes to a cleaner and more organized warehouse space.
Energy-efficient Lighting
Invest in energy-efficient lighting solutions to reduce electricity consumption. Well-lit warehouses improve visibility and safety while lowering operational costs.
Recycling Initiatives
Establish recycling initiatives within the warehouse. Encourage the recycling of materials such as cardboard, plastic, and paper, fostering a more sustainable and organized work environment.
Green Transportation Practices
Implement green transportation practices for inbound and outbound logistics. Choosing eco-friendly transportation options aligns with sustainability goals and contributes to a more efficient supply chain.
Employee Engagement in Sustainability
Promote employee engagement in sustainability practices. Educate staff on the importance of eco-friendly initiatives and encourage their active participation in maintaining a green warehouse.
See also our post on Zen and Clean: A Complete Guide on How to Clean Your Yoga Mat
Continuous Improvement Strategies
Regular Performance Reviews
Conduct regular performance reviews to identify areas for improvement. Evaluate warehouse processes, employee performance, and technology effectiveness to make informed adjustments.
Feedback Mechanisms
Establish feedback mechanisms for employees to voice their suggestions and concerns. Valuable insights from the frontline can lead to improvements in warehouse organization and cleaning procedures.
Benchmarking Against Industry Standards
Benchmark warehouse efficiency against industry standards. Identify key performance indicators (KPIs) and measure your facility’s performance against benchmarks to drive continuous improvement.
Technology Upgrades
Stay abreast of technological advancements and consider periodic upgrades to enhance warehouse systems. Adopting the latest technologies can result in increased efficiency and a competitive edge.
Training for Emerging Trends
Provide training to employees on emerging trends in warehouse management. Staying informed about industry developments ensures that your facility remains adaptable and efficient in the face of evolving challenges.
See also our post on 5 Crucial Benefits of Professional Cleaning Services for Medical Facilities
Conclusion
Optimizing warehouse organization and cleaning is a continuous process that calls for meticulous planning, steady work, and a dedication to continuous improvement. Warehouses can reach their full potential and function at maximum efficiency by concentrating on layout optimization, inventory management, cleaning protocols, employee training, technology integration, sustainability practices, and continuous improvement strategies. These straightforward yet meticulous practices will boost output while also creating a more orderly, safer, and sustainable working environment. As the logistics landscape changes, being proactive in warehouse organization and cleaning will continue to be essential to success.